Estimating costs of production for individual crops can be challenging, but an important practice to understand where there might be areas for savings or investment in better inputs. It becomes even more difficult when there are multiple crops grown on a farm. A new online tool is now available to make it easier. [Read more…]
Commercial Ag Updates + Farm Food Safety
Rutgers Cooperative Extension Ag Agents provide updates on what they see in the field, upcoming events, and other important news that affects your operation, such as developments in on-farm Food Safety. Subscribe if you wish to be notified about workshops, meetings, and upcoming commercial ag events.
Subscriptions are available via EMAIL and RSS.
Ag Irrigation Water Log Template Simplifies Annual Water Use Reporting To NJ DEP
https://go.rutgers.edu/IrrigationLog |
As 2024 winds down and irrigation pumps are finally being shut off after a very long, dry season, thinking about calculating how much water was used to be able to fill out that NJ DEP report form in a couple of months is likely the furthest thing on your mind. However, the RCE Ag Water Use Log Excel Template <https://go.rutgers.edu/IrrigationLog> can make that process much easier, whether you have used it all season, or just need an easier way rather than tabulating all those hours of pumping by hand. [Read more…]
The Rutgers Agrivoltaics Program wraps up its first year of crops research in New Jersey
The Rutgers Agrivoltaics Program is a multidisciplinary group of Rutgers faculty and staff committed to designing and conducting applied agrivoltaics research and outreach for stakeholders in New Jersey and throughout the region.
The Rutgers Agrivoltaics Program (RAP) was initiated over 3 years ago with the signing and passage of the Dual Use Solar Act by the New Jersey legislature. In 2023, agrivoltaics (AV) research installations were established at three Rutgers-New Jersey Agricultural Experiment Stations (NJAES). One at the Clifford E. and Melda C. Snyder Research and Extension Farm in Pittstown, NJ; one at the Animal Farm on the Rutgers New Brunswick (SEBS) Campus, and one at the Rutgers Agricultural Research and Extension Center (RAREC) near Bridgeton, NJ. Members of the Rutgers RAP Team in collaboration the New Jersey Board of Public Utilities, NJ Department of Agriculture, and NJ-DEP are now in the process of implementing the Dual-Use Solar Energy Pilot Program.

Specialty crops being grown in a double panel AV plot at the Rutgers Agricultural Research and Extension Center near Bridgeton, New Jersey.

An image of specialty crops being grown in a single AV panel plot at the Rutgers Agricultural Research and Extension Center near Bridgeton, New Jersey.
The agrivoltaics research at the Rutgers Agricultural Research and Extension Center (RAREC) near Bridgeton, New Jersey was designed to study the effects of agrivoltaics systems on the production of specialty and agronomic crops. This year eggplant, bell pepper, fresh-market tomato, and soybeans were grown under three different treatments: single-axis tracking array with one row of panels, single-axis tracking array with two rows of panels, and no panels (conventional production as a control) to determine the effects of the panels on crop yield and quality.
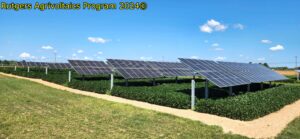
Soybeans were grown in two whole blocks at the Rutgers Agricultural Research and Extension Center near Bridgeton, NJ in 2024.
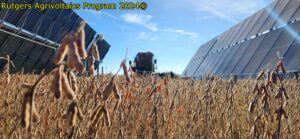
Soybeans being harvested between double AV panel arrays at the Rutgers Agricultural Research and Extension Center near Bridgton, New Jersey.
At the Clifford E. and Melda C. Snyder Research and Extension Farm in Pittstown, NJ the effects of single-axis tracking arrays with one row of panels on forage growth was studied to measure potential impacts on hay yield and quality. There were three cuts of the hay this season along with sampling for forage quality.

Hay being cut in mid-May at the Snyder Research and Extension Farm in northern New Jersey.

Cut hay being wind-rowed at the Snyder Research and Extension Farm in northern New Jersey.
At the Rutgers SEBS Cook Campus Animal Farm in New Brunswick, New Jersey, which hosts equine and livestock facilities, research was done to study pasture forage production and animal grazing patterns in combination with vertical bifacial solar panels. In early fall, four gestational cows (led by Buttercup) were introduced to the AV array research pasture for the first time. The research pasture also includes shelter and drinking water for the animals.
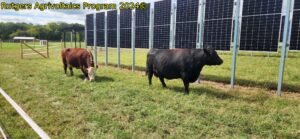
Buttercup (on the right) leading the small herd into the field of vertical bifacial panels at the Cook Campus Animal Farm on the campus of Rutgers University in New Brunswick, NJ.

Buttercup and friends at the watering hole.

The ribbon cutting ceremony held on 30 Sep 2024 at the Cook Campus Animal Farm on the SEBS campus of Rutgers University celebrating the accomplishments Rutgers Agrivoltaics Program.
On 30 Sep., over 80 people attended the Rutgers Agrivoltaics Program ribbon cutting ceremony at the Rutgers Animal Farm in New Brunswick, NJ where State officials, University leaders, and invited guests applauded the research and outreach efforts of the Rutgers Agrivoltaics Program and discussed the potential impacts of agrivoltaics for both the agricultural and solar industries in New Jersey.
Results from all three Rutgers Agrivoltaics Program research sites will be presented at upcoming Extension meetings this winter and spring across New Jersey and the region.
UPCOMING PPRESENTATIONS
Dan Ward will be presenting at the New England Fruit and Vegetable Conference on 18 December 2024 in Manchester, New Hampshire.
Multiple RAP Team members will be presenting in the morning Agrivoltaics Session at the 2025 New Jersey Agricultural Convention and Trade Show in Atlantic City on 5 February at Harrah’s Resort.
More to be announced!
For more information on the Rutgers Agrivoltaics Program and more AV resources please visit the new RAP website by clicking here. Stakeholders interested in keeping up the what’s going on can now subscribe to the new website and have information send directly to their email account. Just go to our contact page and follow the instructions to subscribe!
Articles and images can be used by Permission from the Rutgers RAP Team only – For Permission contact RAP at shawn.sorrels@rutgers.edu.
A New Requirement for Small Businesses (Including Most Farms): Filing a Beneficial Ownership Report with the Department of the Treasury. Deadline is January 1, 2025
There has been a lot of press, and more than a little confusion, regarding a new filing requirement by the US Department of Treasury for any business organized as a corporation, including Limited Liability Corporations (LLC). All corporate businesses are required to file, so don’t throw away that reminder/application that arrived in the mail recently! There are penalties for not filing by the deadline.
The following article is reprinted with permission from Cornell Cooperative Extension as it appeared in the 11/6/2024 CCE VegEdge e-newsletter.
Written by Elizabeth Higgins, Cornell Cooperative Extension Associate in Ag Business Management/Production Economics, Eastern NY Commercial Hort Program, Hudson Valley Research Lab, Highland, NY
Beginning January 1, 2024, most small entities—including single member LLCs—must file online reports with the Financial Crimes Enforcement Network (FinCEN), a bureau of the U.S. Department of the Treasury, disclosing information about the beneficial owners of the entities. This new reporting requirement—estimated to impact at least 32.6 million entities in 2024—was created by the Corporate Transparency Act (CTA). Existing entities have until January 1, 2025, to make their first beneficial ownership information (BOI) report.
Do I have to File?
If you are an LLC, Corporation, LLP or Limited Partnership in New York[NJ], yes you do.
Any entity created by the filing of a document with a secretary of state or any similar office under the law of a state or Indian tribe, unless excepted from the reporting requirement, must file. Examples of exempt entities include tax-exempt and government. (The list of exempt entities is in this FAQ.)
For-profit farms are not on the exempt list. Single-member LLCs are subject to BOI reporting requirements. Sole proprietorship farms are exempt since they do not file with the secretary of state in New York.
Why on Earth do I have to do this?
In 2021, Congress passed the Corporate Transparency Act on a bipartisan basis. This law creates a new reporting requirement as part of U.S. government efforts to make it harder for bad actors to use shell companies or opaque ownership structures to hide or benefit from ill-gotten gains.
What Happens if I Don’t File?
You should file because the penalties are large, and it is straightforward to file.
Failure to file a BOI report can result in severe civil and criminal penalties! If you don’t file a BOI report, you could face a $500-per-day fine, up to $10,000, and up to two years in prison.
==> Where to File: https://boiefiling.fincen.gov/fileboir.
How will this information be used and who can see it?
Beneficial ownership information reported to FinCEN is exempt from disclosure under the Freedom of Information Act (FOIA). FinCEN published the rule that will govern access to and protection of beneficial ownership information on December 22, 2023. According to the website, beneficial
ownership information reported to FinCEN is stored in a secure, non-public database using rigorous information security methods and controls typically used in the Federal government to protect non-classified yet sensitive information systems at the highest security level.
In accordance with the Corporate Transparency Act, FinCEN may permit access of beneficial ownership information to:
- Federal agencies engaged in national security, intelligence, or law enforcement activity.
- State, local, and Tribal law enforcement agencies with court authorization.
- Officials at the Department of the Treasury.
- Foreign law enforcement agencies, judges, prosecutors, and other authorities that submit a request through a U.S. Federal agency to obtain beneficial ownership information for authorized activities related to national security, intelligence, and law enforcement.
- Financial institutions with customer due diligence requirements under applicable law (to facilitate compliance with those requirements).
- Federal functional regulators or other appropriate regulatory agencies that supervise or assess financial institutions with access to beneficial ownership information (to supervise such financial institutions’ compliance with customer due diligence requirements).
What Information Will I have to Provide?
For the company:
- Full legal name
- Any trade name or “doing business as” name
- Complete current U.S. address
- Jurisdiction of formation (including State or Tribal jurisdiction for a domestic reporting company)
For each beneficial owner and each company applicant required to be reported:
- Full legal name
- Date of birth
- Complete current address
- Unique identifying number and issuing jurisdiction from one of the following non-expired documents:
- U.S. passport
- Identification document issued by a State, local government, or Indian Tribe
- State-issued driver’s license
- If none of the above are available, a foreign passport, and an image of the document from which the unique identifying number was obtained.
What is a “Beneficial Owner”?
In general, beneficial owners are individuals who:
- Directly or indirectly exercise “substantial control” over the reporting company, or
- Directly or indirectly own or control 25% or more of the “ownership interests” of the reporting company.
The rules for the program provide that beneficial owners do not include:
- A minor child, provided the reporting company reports the required information of a parent or legal guardian of the minor child and states that the individual is the parent or legal guardian of a minor (once the minor child reaches the age of majority, the report must be updated).
- An individual acting as a nominee, intermediary, custodian, or agent on behalf of another individual.
- An employee of a reporting company, acting solely as an employee, provided that such person is not a senior officer.
- An individual whose only interest in a reporting company is a future interest through a right of inheritance.
- A creditor of a reporting company.
What are “Company Applicants”?
Companies created or registered before January 1, 2024, are required to report only beneficial owners. Companies created or registered on or after January 1, 2024, must report the company applicants, in addition to beneficial owners. Company applicants include:
- The individual who directly files the document that creates, or first registers, the reporting company; and
- The individual that is primarily responsible for directing or controlling the filing of the relevant document.
What is the “FinCen Identifier”?
An individual or reporting company may obtain a FinCEN identifier by submitting an application at or after the time that the reporting company submits its initial report. Each identifier is specific to the individual or reporting company. If an individual has obtained a FinCEN identifier, the reporting company may use that identifier in its report instead of reporting all of the required information for the individual.
Where Can I get More Information?
- Department of the Treasury, Financial Crimes Enforcement Network (FinCen) Beneficial Ownership website: https://www.fincen.gov/boi
- Department of the Treasury, Financial Crimes Enforcement Network (FinCEN) BOIeFiling website: https://boiefiling.fincen.gov/
Produce Safety Rule Training
The registration deadline is fast approaching for our December 5 and 6, 2024 Remote Food Safety Modernization Act: Produce Safety Rule Training. This training fulfills the requirements of the Food and Drug Administration that at least one person from each farm that produces fresh fruits and vegetables needs to receive a standardized curriculum recognized by the FDA. This class runs from 9:00-1:00 EST and both days are required to receive the certificate. The deadline to register is Sunday, November 17, 2024, exceptions to this deadline cannot be made due to the nature of the remote program and the need for participants to have a copy of the Growers Training Manual prior to the training. Without the manual at the time of training participants will not receive a certificate. Manual will be mailed to all registered participants. For more information and to sign up for the class go to https://onfarmfoodsafety.rutgers.edu/trainings.
Financial Assistance for Food Safety Certification and Training
This is the chance for eligible fresh fruit and vegetable growers to recover some of their expenses for implementing food safety practices on their farms.
For 2024:
- Applications are due between July 1, 2024 and January 31, 2025
- Eligible expenses must be between June 26, 2024 and December 31, 2024
For 2025:
- Application is due between January 1, 2025 and January 1, 2026
- Eligible expenses must be between January 1, 2025 and December 31, 2025
Eligible specialty crop operations can apply for Food Safety Certification for Specialty Crops (FSCSC) by working directly with the Farm Service Agency offices at your local FSA office for details. Applications will be accepted via mail, fax, hand delivery, or electronic means.
How the Food Safety Certification for Specialty Crops Program Works
The FSCSC program provides financial assistance for specialty crop operations that incur eligible on-farm food safety program expenses related to obtaining or renewing a food safety certification in years 2024 and 2025. This program helps offset costs to comply with regulatory requirements and market-driven food safety certification requirements. FSCSC will cover a percentage of the specialty crop operation’s cost of obtaining or renewing their certification, as well as a percentage of their related expenses.
Program Eligibility
Eligibility requirements for FSCSC applicants are outlined below. We recommend you review these requirements before initiating your FSCSC application.
To be eligible for FSCSC, an applicant must:
Have obtained or renewed:
- 2024 food safety certification issued between June 26, 2024, and December 31, 2024
- 2025 food safety certification issued during calendar year 2025.
- Be a specialty crop operation (growing fresh fruits and vegetables); and meet the definition of a small business or medium size business.
- A small (farm) business means an applicant that had an average annual monetary value of specialty crops the applicant sold during the 3-year period preceding the program year of not more than $500,000.
- A medium (farm) business means an applicant that had an average annual monetary value of specialty crops the applicant sold during the 3-year period preceding the program year of at least $500,001 but no more than $1,000,000.
Category of Eligible Expenses | Payment Amount of Eligible Costs |
Developing a Food Safety Plan for First Time Certification | · 75% (no maximum) |
Maintaining or Updating a Food Safety Plan | · 75% up to $675 |
Food Safety Certification | · 75% up to $2,000 |
Certification Upload Fees | · 75% up to $375 |
Microbiological Testing of Produce | · 75% up to 5 tests |
Microbiological Testing of Soil Amendments | · 75% up to 5 tests |
Microbiological Testing of Water | · 75% up to 5 tests |
Training Expenses | · 100% up to $500 |
FSCSC payments are calculated separately for each category of eligible costs based on the percentages and maximum payment amounts. The FSCSC application and associated forms are available online at farmers.gov/food-safety.
You are encouraged to contact the Farm Service Agency office about FSCSC, program eligibility, or the application process. You may also call 877-508-8364 to speak directly with a USDA employee ready to provide one-on-one assistance.
For our current trainings please go to: Our Trainings – Rutgers On-Farm Food Safety